About Fred V Fowler
Catalogue Pages
|
 |
|
Holematic Bore Gage Improves
Accuracy on F-22 Fuselage
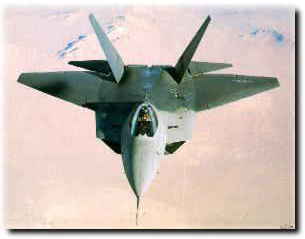 |
Lockheed-Martin
Gets .00015" Accuracies For New F-22 Fighter Program
Fort Worth,
Texas,- Sometimes the inability to drill or ream a hole
accurately can make or break the functioning of a high technology
aircraft, according to a manufacturing engineering specialist
with Lockheed-Martin Tactical Systems in Fort Worth.
|
Here,
where the main fuselage section of the Air Force's new F-22
fighter is being assembled, accuracy is a critical factor
because of the exotic metals and other materials used in the
successor aircraft to the well known F-15 fighter.
Fred V. Fowler
Co. is supplying that needed accuracy!
Materials
being drilled at the plant for both the F-22 and the F-16
include titanium/composite stacks as well as aluminum. "This
is tricky," says Todd Lazar, "because the tolerances involved
in assembling the new aircraft are much tighter than on the
F-16. It's also more difficult to drill through a stack of
composite materials."
He
explained that the drill first bores through the composite
and then into the tough titanium, which can easily cause an
enlargement of the first hole. To be sure the bored hole is
precise, accurate measurement is absolutely necessary. "Until
recently," he adds, "we haven't been able to access the different
drilling depth levels with any degree of ease or precision
to make the measurement." Previously, several methods were
used for inspection, including dial bore gages and plug gages,
but the results were imprecise.
|
New
Holmatic Bore Gage |
After
acquiring the Holematic Mark II Pistol Grip instrument from
Fowler/Bowers, however, Lazar indicates that his group can readily
inspect the different levels in the layered materials. |
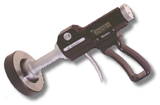 |
|
With
the new Fowler instrument Lockheed-Martin is obtaining accuracies
to 0.00015" on the F-22, which the Air Force plans as its major
air-to-air weapon. The Fort Worth plant assembles sections of
both the F-16 and the F-22, which are produced at three other
facilities.
"Using the new
Pistol Grip, we make our
measurements three times faster. We estimate that we can measure
18 holes per minute with desired repeatability. Formerly,
we could only measure six holes each minute on the F-16. And
the setup times for both methods are the same," Lazar says.
Covering
a standard range from .040-12" (1-300mm), the Holematic Mark
II Pistol Grip bore gage has improved electronics which include
direct RS232 output, two preset memories, preset recall, tolerancing
functions, and .00005"/ .001mm resolution. It has tungsten
carbide measuring anvils on all 3-point, quick self-centering
heads.
|
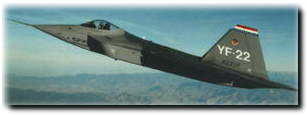 |
Simplified
Training
Lazar
says that after the instruments are assembled in the gage
kits as desired, with the proper presets in the gages memory,
operator training is "exceedingly simple." It takes approximately
10 minutes of 'hands on' training to become proficient with
the gages for Lockheed-Martin's application.
|
|
Training
is thus "at least twice as fast" compared to more complex
gages. "You push once to activate it, then insert the probe
into the ring gage, push the same button a second time, which
presets out the gage, and, after placing the probe in the
hole, you are ready to measure."
Lazar
also reports Lockheed-Martin is working with Fowler and British
Indicators to develop a gage for measuring panel-to-panel
flushness of gaps, which is vital for successful operation
of the aircraft under all conditions. "The seams between fuselage
panels have to be perfect," he says. The special gage developed
by the two companies has replaced feeler gages.
|
ami
|
|