About Fred V Fowler
Catalogue Pages
|
 |
|
Checking System and
SPC Improve Gage Studies
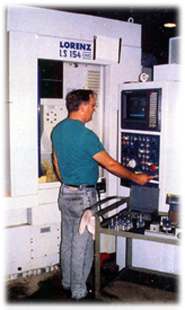 |
Fairfield
Manufacturing, October 1996
To attain the
high precision part quality needed by gear manufacturers,
ISO 9001 certification is not always enough. In the case of
Fairfield Manufacturing Company, Inc., QS 9000 plus a range
of industry specifications, in addition to the special needs
set by individual customer companies, are more the quality
norm for this largest independent North American producer
of a broad range of loose gears and complete power transmission
assemblies.
Currently, the
company produces more than 10,000 different part numbers totaling
about two million gears ranging in size from 1 to 60" in diameter.
|
|
Gage
Repeatability and Reproducibility |
For Fairfield,
which has been able "to reduce costly, post-production inspection,
the major challenge has been to increase our on-line measuring
capabilities so that we can have optimum control of our manufacturing
process in order to meet the multi-level goals of our customers,"
says Dan Phebus. Director of Quality. - In turn, we make our
customer assembly operations more reliable because the gears
conform precisely to their own design drawings. We believe
that GR&R is the key to reducing both our own and other users'
variations."
By increasing
its measuring capabilities, Fairfield has made major gains
in preventing variations through better process control, significantly
reducing rejects by correcting the manufacturing process beforehand.
Highly accurate instrumentation became necessary to succeed.
Through its Production Part Approval Process (PPAP), Fairfield
bolstered its GR&R program. "We had to verify the process
statistically. That would allow us to meet the rigorous tolerances
we not only set for ourselves but which were critical for
our customers," Phebus says.
The key instrument
first acquired in 1992 was a Fowler/Trimos Mini-Horizontal
Measuring System which enables Fairfield to measure
both internal and external gear parts accurately in one pass.
It replaced "mikes and pins," which caused gage errors of
25% or higher "under ideal conditions," he adds, More recently,
five more Mini-Horizontals have been acquired.
|
In
House Studies to Process Control |
Phebus
says the company had conducted an intensive in-house study on
gaging errors. For example, it found that measuring a part with
a total tolerance of 0.0018. made with 3"- 4" micrometers and
calipers. primarily hand-held tools, showed a gage error of
51.7 %, with column-mounted "mikes and pins" a 33.7% error. |
|
However,
when using its new Mini-Horizontal Measuring
System only a 7.4% error was evident. |
|
This is why, Phebus
says "today's measurement capability has to exceed production
process capability. We have transformed our operation from post-production
inspection to on-line process control, reaping the twin benefits
of better quality improvements and cost- reductions." |
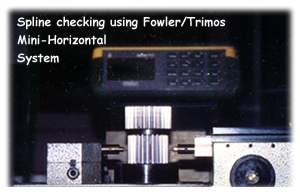 |
How
this was accomplished was due in large part to an idea of Ron
Gellenbeck, the company's chief tool designer, who suggested
putting the Fowler/Trimos instruments on movable carts adjacent
to the production line. This was a superior and quicker way
to get results than by trucking over the finished gears to an
inspection laboratory. "We did it all on-line and thus could
immediately detect variations. Then we could alter the process
to gain the uniformity that was our goal." |
High
Volume Measuring... |
Fairfield's basic
business is gears and power transmission systems for OEM customers
manufacturing off-highway and construction equipment, mining,
railroad, agricultural, industrial and material handling equipment
of all kinds. This makes big demands on its products' accuracy
and conformance to design specifications. "We have a high volume
of gears to be measured and sorted according to gear size," says
Gellenbeck. "They are boxed and shipped by classifications, and
some of our customers require reverse classification. This means
that the smaller gear pitch diameter needs a larger code number.
In contrast to all other instruments on the market, the Fowler/Trimos
Mini-Horizontal System can handle the correct size code in
reverse order.
In addition, he
explained, the stable base of the Mini-Horizontal units complemented
the movable cart system Fairfield had devised to per- form the
on-line measurements prior to heat treating the gears and the
grinding operations.
|
Six
primary benefits of the new system have resulted: |
- Obtaining a
true process control technique.
- Saving substantial
amounts of time over post-production inspection.
- Reducing customer
assembly time.
- Significant
dollar savings for the process by reducing rejects and producing
faster verification of part sizes.
- Better human
relations in the plant, because measurement operators like
the ease of using the system, encountering less fatigue
than before.
- The new ability
to measure both externally and internally. The latter advantage
was achieved by Fairfield technicians who expanded the utility
of the Trimos instrument and its Sylvac probe by devising
new anvils to measure gear sizes up to 12"in diameter.
|
Ruggedness,
Reliability and Accuracy! |
Gellenbeck adds
that the original selection of the instrument depended heavily
on its 0.00006"accuracy and the fact that the anvils were removable
and thus could be replaced with ball-type or cylindrical pins
to measure pitch diameters, The system has a Sylvac
1" travel probe and a digital readout display box. A direct
two-way RS-232C data output allows connection to a printer.
"With this gage,"
concludes Phebus, "we detect variations quickly and simply
and are sure we're not getting false signals about our process."
The company is continuing to refine its SPC program and improve
the accuracy of its instrumentation, since they are mutually
dependent for ultimate product precision.
|
ami
|
|