About Fred V Fowler
Catalogue Pages
|
 |
|
New Instruments Cut Quality Costs 20%
Hytrol
Extends Lead in Conveyor Systems: New Instruments Give 20%
Reduction in Quality Cost. |
Jonesboro,
Arkansas-With its new Quality Laboratory in full swing,
Hytrol Conveyor Company-the largest producer of conveyor hardware
in North and South America-is assuring its top position in
the field by focusing on having the latest and most advanced
metrology instruments as well as reinforcing its guaranteed
24-hour shipment policy. It serves a broad range of industries-from
producers of electronic equipment, food and retail stores,
to rubber products, beverage and computer manufacturers. |
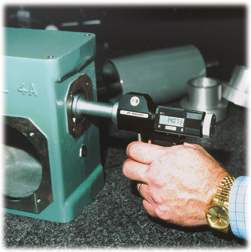 |
Checking
the bore of bearing on the input shaft of a reducer housing. |
|
The
company's success, based on a strong distributor network and
responsive customer service, continues to lead the industry
because of its emphasis on streamlining the flow of materials
and better integration of its manufacturing process. Much
of the focus today is on conveyor quality, and the new Quality
Lab is a key factor in assuring flaw-free manufacturing. Recently
Hytrol conducted a complete accuracy check on its laboratory
shop tools, among them a broad range of Fowler Swiss and British-made
height, depth, and bore gages, pin and gage block sets and
digital hardness testers. |
|
Fowler/Bowers
on the Job |
For the high
precision functioning of its conveyors, Hytrol's reducer
manufacturing operations, in which the housings require
tight machining tolerances of .001" (with a plus and minus
range of .0005"), are critical. This means high accuracy
in measuring parts. Of special help have been the Fowler/Bowers
pistol-grip bore gages. "These give us SPC compatibility
for our CNC machining operations," according to Sam Wright,
Manager of Hytrol's Technical Design Support. "The older
model bore gages can no longer meet our needs."
To machine out
the rollers for the precision bearings mounted on the rollers
that are responsible for the smooth functioning of its conveyor
systems, as well as the 21Ý4" diameter press-in bearings
in its pulley tubes, advanced digital micrometers and calipers
play a critical role.
Wright explains:
"The smaller the diameter of the pulley, the more RPM it
experiences. Because steel parts are so small today, we
can't use cast iron bearings, which are too large. A precision
pulley needs an instrument like the Bowers pistol grip gage.
Bowers bore gages employed by Hytrol have a range of 3Ý4-4",
4-5" and 5-6".
|
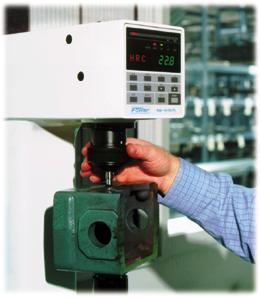 |
Wright explained
that the quality auditors, who used to work on the shop
floor to check on initial specification settings for the
machinery, now can do much more precise work in the new
Quality Laboratory environment. "The lab gives us a good
back-up for the on-line checking operations," Wright added.
"The next step we plan is to have full-time technicians
in the laboratory which will relieve the auditors to expand
their checking work."
As part of its
overall efficiency plans, this past July 50-year old Hytrol
had Rockford (Illinois) Calibration Services certify all
the company's tools, a process that will be repeated next
year.
|
Fowler's
hardness tester is used in checking a cast iron reducer housing. |
Overall,
Wright says, the more accurate new measuring instruments and
systems now being used by the company are on record to have
"reduced our cost of quality by 20%, by virtue of the drastically
reduced remake work and improved product quality. We have
been measuring these results of our quality efforts for more
than two years." |
ami
|
|