The scale
and scanning unit of sealed linear encoders are protected against harsh machine
shop environments by an aluminum housing with flexible sealing lips. These
linear encoders are ideal for all manual and NC machine applications as well
as all metal forming and wood working machines. The sealed linear scales come
in several size configurations as well as lengths (over 30 meters for a single
axis). Accuracy ranges from ±10 µm to ±2 µm. Reference
marks come in standard or distance-coded versions.
Exposed linear
encoders operate with no mechanical contact between the scanning head and
the scale. This eliminates any mechanical backlash or hysteresis. The measuring
standard for all exposed linear encoders is a phase grating applied to a carrier
of steel or glass. Applications include high accuracy test and measurement
machines, manufacturing machines related to the electronics industry, and
ultra precision machines such as diamond lathes, and facing lathes. Several
accuracy grades (to ±0.1 µm) and size configurations (lengths
to over 30 meters) as well as standard or distance-coded reference marks are
available.
HEIDENHAIN
Digital Readouts are used for displaying linear and/or rotary position when
used in conjunction with HEIDENHAIN encoders. DRO's are available with one
to four display positions with resolutions from 10 µm to as fine as
5 nm. Typical functions available include distance-to-go, min/max display,
program storage, RS-232-C output, tool memory, datum shift, and graphic help
screens to name a few. DRO's are typically retrofitted on manual metal-cutting
and metal forming machines, measuring and inspection machines, as well as
electrical discharge machines.
HEIDENHAIN RETROKIT digital readouts can be retrofitted to knee mills and
lathes. Regardless of specification, size or whether you're installing on
new equipment or retrofitting machines already in operation, HEIDENHAIN offers
RETROKIT Digital Readouts (DRO) to improve machine accuracy and parts precision.
Rotary
encoders serve as measuring sensors for rotary motion, and for linear motion
when used in conjunction with mechanical measuring standards such as
leadscrews.
Areas of application include: electrical drives, machine tools, printing presses,
woodworking machines, and robots and handling devices. HEIDENHAIN rotary encoders
convert rotary motion to electrical signals by photoelectrically scanning
DIADUR circular graduations. The measuring signals are evaluated either in
numerical controls (NC) and programmable logic controllers (PLC), or simply
in a digital position display unit. Thanks to its wide range of mechanical
and electronics features, the HEIDENHAIN rotary encoder program offers the
suitable rotary encoder for virtually any application from simple positioning
tasks to the highly dynamic control of electrical drives.
Angular
Encoders provide system accuracy as fine as ±0.4 arc seconds. These
encoders are, therefore, ideal in applications such as rotary tables on machine
tools, indexing tables, swivel heads, antennas, observatories, scanners, and
measuring equipment. Several different mechanical variants are available to
accommodate mounting configurations. Angular encoders are provided with shaft
or hollow through shaft with integral coupling. Modular angular encoders are
also available for mounting directly on a spindle.

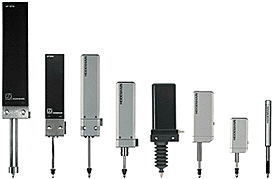
METRO Digital Length Gauge Systems are used for precise length measurement
of single components and work pieces in the shop or in measuring laboratories,
for inspection machines and NC machines, or for position readout with X-Y
tables, and translation stages. They also serve as position encoders in automated
production facilities and testing stations, among others. METRO comes in various
measuring ranges, (from 12-101 mm) and are available in accuracies of ±1µm,
±0.5µm, and ±0.2µm.
CERTO gauging system is HEIDENHAIN's high accuracy gauging station for measuring
high precision components, and as a calibrating device for special purpose
machines and gage blocks. The accuracy of the CERTO system is ±0.03
µm, and is available with a 25 or 60 mm measuring range.
Machine
tool builders and operators need measuring systems that provide detailed information
on machine accuracy with a minimum of time spent on mounting and adjusting.
HEIDENHAIN offers three measuring systems that meet these requirements: The
KGM 182 grid encoder for circular path, irregular path, and dynamic tests,
The DBB 110 double ball bar system for circular test with large radii, and
the VM 182 comparator system for measuring position accuracy and guideway
error on linear axes. Also available from HEIDENHAIN is the ACCOM software
for measurement evaluation which is used in conjunction with all three measurement
devices. ACCOM supports WINDOWS 95/98 and 2000/NT 4.0.
HEIDENHAIN
offers a wide variety of straight cut controls with four axes measuring, and
contouring controls for up to nine axes. HEIDENHAIN controls feature dialog
prompted conversational programming, and full color graphics capabilities.
CNC controls are used for milling, drilling, and boring machines, as well
as EDM's, large machining centers and lathes. Also available are controls
offered with complete integrated drive control, motors, and digital drives.
Accessories include 3-D touch probes, and digitizing software.
3-D
touch probes from HEIDENHAIN were conceived for use on machine tools - particularly
for milling machines and machining centers. 3-D touch probes help to reduce
setup times, increase machine utilization rates, and improve the dimensional
accuracy of the finished workpieces. Setup, measuring and inspection functions
can be conducted manually or - with most NC controls - under program control.
The trigger signal is formed by an optical sensor, which functions without
wear, and is very reliable.