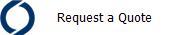
GO-NO GO GAGES
The concept of Go-No Go gaging is so simple in its logic
that it has been known to delight philosophers. For them, a Go-No Go
situation is the very rare case where there are only two alternatives - black
and white - with no gray in betwee- n. In practice it is not quite so simple
as this, since there are a few borderline cases which require a little human
judgment. But the ground rules for using the cylindrical plug gage are
certainly not complicated. If the Go end of the gage slips through the
hole and the No Go will not enter, this is necessary and sufficient proof that
the hole is within the tolerance limits assigned to it. Pick up the taperlock plug gage and examine it. This gage was made to inspect the hole
which the design engineer specified must be .500" +- .002". The GO member of
the gage is therefore no smaller than .498-inch, the low limit of the
hole tolerance. The NO GO member is no larger than .502-inch, the
high limit.
Now the question naturally arises, "How much larger than.
.498-inch can the GO end of the gage be? And how much smaller than
.502-inch can the NO GO be?" In other words, how much tolerance can
the gage maker be allowed? Though he may spend many tedious hours
finishing off a piece of work like a jewel, he still works under the same
natural laws as the man with a boring tool. He must have some tolerance
too. The generally-observed rule-of-thumb, which has some statistical
reasoning behind it, is that the gages can have a total tolerance no greater than
ten percent of the part tolerance. In the case of the
.498"/.502" hole, a
total tolerance of .004-inch has been allowed. Then the overall tolerance
permitted for the gage cannot be more than .0004-inch, which must be distributed
between the GO and NO GO members. Splitting it evenly between them would
be permissible. The GO diameter could have the limits
.4980"/.4982" and the
NO GO .5018"/.5020".
There are ways of dealing with the permitted gage tolerance
which will seem quite logical when the life cycle of a fixed limit gage is
better understood. As an example, the idea of a wear allowance on
the GO member should be studied by those who plan to go into quality control
work. For the present, let us settle for the fact that the gage in hand
was made to one of the several classes of tolerance which have been
adopted and standardized by American gagemakers. Class Z, the coarsest of
the standard tolerances, permits the gagemaker to deviate .0001-inch in one
direction only on each of the gage members. So in this case, the GO
member can be .0001-inch larger than .498" and the NO GO can be
.0001-inch smaller than .502". When the tolerance is thus
restricted to one side of the "name" size, with none permitted on the
other, it is called unilateral tolerance. When tolerance is
permitted on either side, it is called bilateral.
In the future, metric dimensions will probably appear with
increasing frequency on American drawings. This is not a serious problem
in dealing with simple linear dimensions like these, where conversion factor:
one inch = 2.54 centimeters = 25.4 millimeters can be used. Metric threads
do present a sticky conversion problem as will be seen in discussion of threads.
Since the very small decimal numbers which must be used in
discussing gage tolerances will be new to some readers, it may be helpful to
know what they are called in the language of the machine shop.
.001" one thousandth (of an inch)
.0001" one tenth (of a thousandth)
.00001" ten millionths
.000001" one millionth
Using this vocabulary, then, the figure .00012" is read
"one tenth and twenty millionths." Standard gagemakers'
tolerances for cylindrical gages up to .825-inch in diameter are as follows:
Class XX .00002" (twenty millionths)
Class X .00004" (forty millionths)
Class Y .00007" (seventy millionths)
Class Z .0001" (one tenth)
|